Recomendaciones en la bomba centrífuga y de alimentación de la caldera
En sistemas de caldeo que trabajan con presiones altas, hay algunas cuestiones que se deben revisar en todo momento, sobre todo si se desea garantizar la conductividad del agua desde la bomba de alimentación, hasta los tanques y salidas de todo proceso industrial.
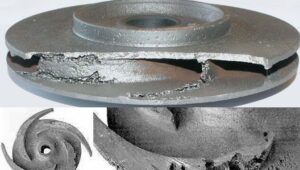
Primero hay que checar posibles rompimientos debido a corrosiones, cuyas dosificaciones de sodio podrían llevar a tensiones exageradas en todas las líneas. Se supone que en un boiler industrial que labora con altas presiones, el límite máximo es circundante a las 25 partes por billón para sistemas que operan con presiones por arriba de los 42 kg/cm2 (600 psi).
Para hacer las mediciones correctas del sodio en el sistema de caldeo, es necesario analizar el vapor de las turbinas, con componentes hechos a base de electrodo de iones; de esa manera se sabrán los contenidos para limitarlos a sus niveles pertinentes.
Ahora, las causas que se pueden enumerar cuando los niveles de sodio permisibles, comúnmente son derivados de alguna fuga en el sistema de condensación, filtraciones en los lechos de refinado, así como desperfectos en los componentes desmineralizadores. De hecho, los encargados en la fabricación de turbinas para boiler industrial de alta capacidad, tienen especificaciones muy claras, de los límites admisibles de sodio en dichos equipos, que nunca sobrepasen las 5 partes por billón y en el proceso, se busca el material adecuado para que opere de manera óptima en condiciones extremas, como cualquier sistema de caldera que labora con presiones altas, y con altos riesgos de agrietamientos y elementos corrosivos que atentan constantemente contra los metales.
En el caso de calderas pirotubulares antiguas, es necesario checar en todo momento que no surjan combados en la parte baja de la tubería, más propiamente en sus refuerzos. Esto pasaría cuando la virola se dilata al calentarse demasiado, alargando dichos refuerzos, y si después de eso, repentinamente se enfría, entonces provocará un combado que afecta esa parte importante del sistema.
Cómo anticiparse a una cavitación o efectos hidrodinámicos en una bomba de alimentación del boiler industrial
Una cavitación en términos generales, se refiere a un efecto hidrodinámico que se crea a partir de cavidades de vapor dentro de un fluido en estado líquido, cuyas fuerzas encontradas reaccionan a diferentes presiones y velocidades. En ese sentido, dentro de un equipo de caldeo, la aspiración de vacío es presionada por las altas temperaturas que se suscitan en la red. Esto lleva a varios eventos, siendo tal vez el peor, un posible golpe de ariete, que llevé a martilleos constantes en los metales, sobre todo de tubería y bombas centrífugas, llevando a roturas y paros costosos; la bomba alternativa es una de las más afectadas por embalado.
Asimismo, la bomba de centrífugos aumentará su temperatura a niveles alarmantes, con vibraciones y ruidos excesivos. Para corregir dichos eventos, requerirá de una mayor presión de aspiración, o temperaturas de operación mucho más bajas. Y para una prevención más anticipada, lo más sensato sería hacer fluir corrientes de agua con baja temperatura. Si al menos se necesita de una medida temporal, habrá que reducir la velocidad de fluidos, cerrando la descarga de la bomba centrífuga, con una reducción de la temperatura de fluidos.
Las purgas en los sistemas de boiler industrial son de gran importancia, puesto que un eventual fallo en los purgadores, o que estos componentes sean de calidad cuestionable, entonces habrá cavitaciones, cuyos vapores soplarán a través de los depósitos del agua. Esta es una causa recurrente de temperatura de aspiración excesiva.
Esto lleva a un tema de las válvulas de purga en el boiler industrial compacto. Para prevenir operatividad y rendimiento en esta clase de sistemas, será necesario emplear líneas de bypass, o en su defecto, abrir un poco los purgadores. Otra opción para prevención operativa, es actuar ante una eventual formación de hielo en la parte del sistema.