Examinar las partes de una caldera para prever posibles fallos durante la operación en aplicaciones de producción o en el servicio de agua caliente sanitaria, siempre va a ser complicado, sobre todo en aquellos sistemas de vapor que trabajan durante largos periodos en un entorno industrial. Hay que estar al pendiente de estos detalles en todo momento.
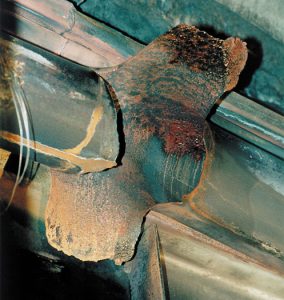
Un ejemplo claro es, que cuando notamos que la tubería del sobrecalentador empiezan a presentar fallas que invariablemente afectan al sistema, probablemente sea porque los depósitos han sido arrastrados hasta ese lugar, originados en el agua del tanque de caldeo, donde posiblemente hubo algún estancamiento. También los tubos pueden sufrir corrosión, pero es un síntoma que pasa muy raramente; suelen ocurrir cuando la caldera está detenida por un tiempo determinado.
Los depósitos son esencialmente peligrosos en todas las partes del boiler industrial, porque se acumulan debido a sus espumas y arrastres. Los álcalis y otras sustancias suspendidas en las aguas, deben eliminarse o al menos, disminuirse por medio de purgas más intensas y extensas. Cuando existen contaminantes orgánicos en el sistema de caldeamiento, lo mejor será hacer un pretratamiento o incluir separadores de aceite para que el agua no las arrastre. Hay que estar al pendiente de los aditivos de tales contaminantes, porque estos son los que arrastran las suciedades que se acumulan en los depósitos.
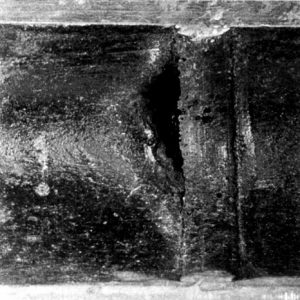
Bajar los niveles del agua en el boiler industrial, es primordial para obtener un correcto control en los niveles de carga. Estar al tanto de esto, evitará que haya presencia de partículas dañinas en el sobre-calentador, que posteriormente forman los lodos debidos al arrastre.
La inanición que provoca muertes en áreas cerradas con equipos de caldeo, es porque estos mismos trabajan con una tasa disminuida, lo que es realmente inadmisible. Si en el lapso de esos arranques bajos, se nota un incremento de la temperatura de forma súbita, en dicha área cerrada, quiere decir que la caldera no ha agarrado la presión que se precisa en el arranque, por lo tanto, no habrá suficiente vapor para enfriar la tubería.
Cuando se presentan roturas en las líneas de conductos, ya sea por deformaciones o tensiones en la estructura, se deben reparar, pero estando conscientes de que el daño puede estar presente a lo largo de toda la tubería, pero que es posible que a simple vista no se vean, ya que suelen ser marcas muy finas. Se puede reemplazar todo el conducto, o por medio de reconstrucción localizada en puntos específicos, mediante
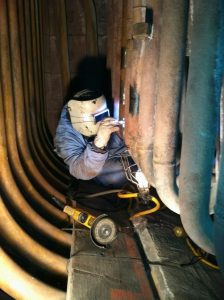
un corte de secciones tubulares, para luego soldar la circunferencia cortada. En estos casos también se requeriría de una inspección más avanzada, a través de tratamientos que impliquen un pre y pos calentamiento. Las opciones son varias, con una elección dependiendo de los diagnósticos concienzudos.
Los agujeros de los tubos, en ocasiones se escorifican o disminuyen sus diámetros, por los daños de tensiones o presiones desmedidas. En ese sentido, es fundamental hacer un corte o rebaje en el mismo conducto, para que vuelva a adaptarse a la línea de tubería, ya sea en una estructura de humos o de agua. Desechar tubos que ya no sirven, para poder adaptar otros, se hacen a través del mismo achaflanado.
Los extremos de los tubos de un sistema de boiler industrial, tienen que soldarse adecuadamente, con sus refuerzos hechos a base de cobre que permitan una soldadura firme, pero sin que haya fundiciones, que imposibiliten una posterior remoción sencilla de las conexiones entre tuberías. A final de cuentas, se debe hacer un achaflanado correcto, con los espesores adecuados y con anillos de acero que embonen perfectamente con calderas que tengan tuberías de humos.